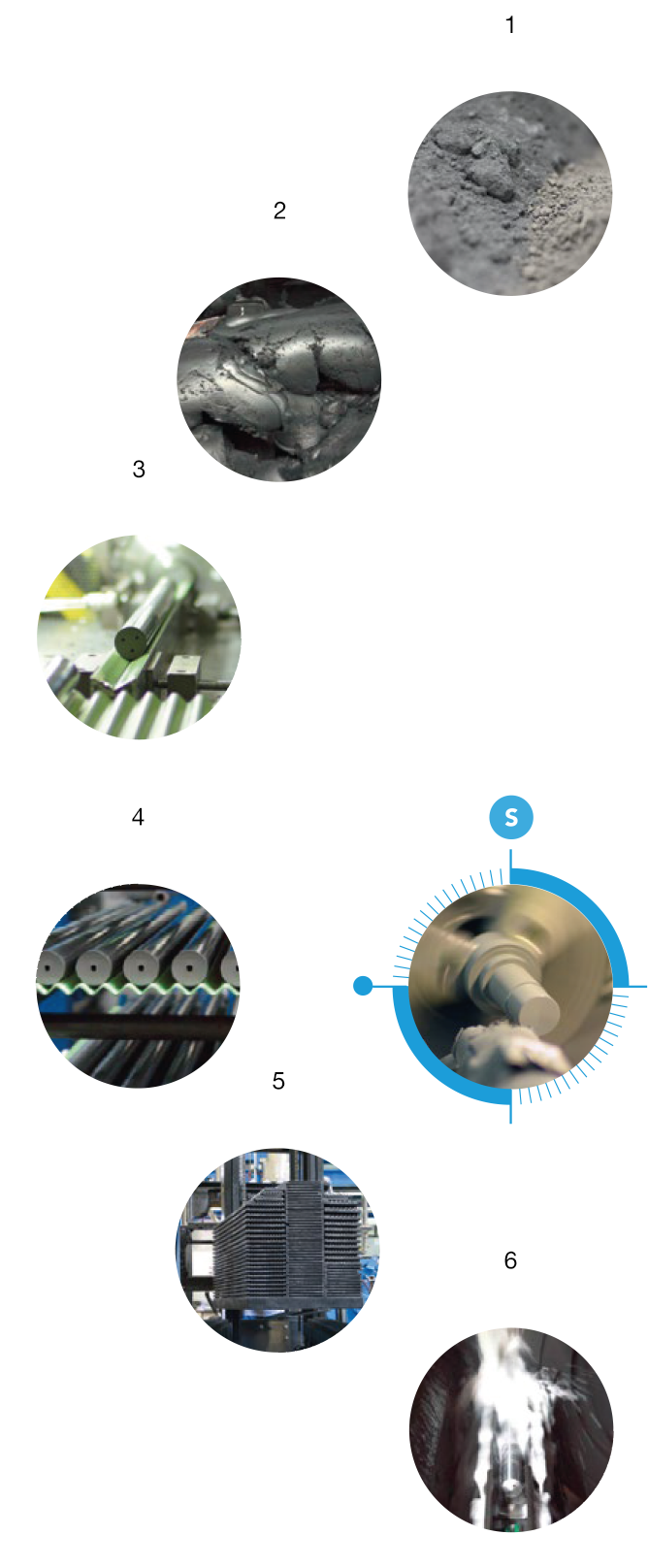
At the beginning WC, Co and doping elements are mixed according to our special recipes. This mixture is then ball-milled for several hours and afterwards sieved for an outstanding homogenous distribution of carbide grains of the specific grade powder.
With the help of organic additives, the powder is plasticized in our kneaders into a clay like dough that can be extruded.
Through our patented production technology the plasticized mixture is then extruded. Thereby coolant ducts with different helical angles and geometries can be realized in our round rods.
Subsequently, part of the added liquids must be slowly removed from the product under strictly controlled conditions in our climate chamber and special drying-furnaces. The drying time depends on the outer diameter.
Main and counter spindle, two turrets, six linear and two round axes as well as a specially adapted
bar loading and part removal system – with these prerequisites, preforms can be produced
fast, economical and reliable to meet customer requirements.
At the beginning, the residual plasticizers evaporate during the dewaxing process. After further heating, the Co melts at about 1380 °C and flows into the free spaces between the WC grains. Through the hot-isostatic process, the remaining porosity is removed and the product subsequently cooled. The cemented carbide products lose up to 25% in volume during the whole Sinter-HIP process.
After passing a last rigorous inspection the rods are then either stocked in our warehouse or refined in our centerless-grinding department.
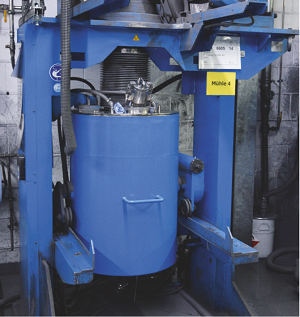
Mixing, Milling, Sieving
At the beginning we mix WC, Co and doping elements according to our special recipes. This mixture is then ball-milled and sieved for an outstanding homogenous distribution of carbide grains of the specific grade powder.
Kneading
With the help of additives, we then plasticize the powder into a clay like dough in our kneaders. This step is necessary to shape the final product.
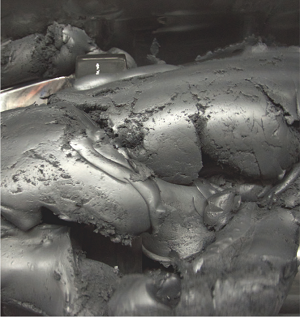
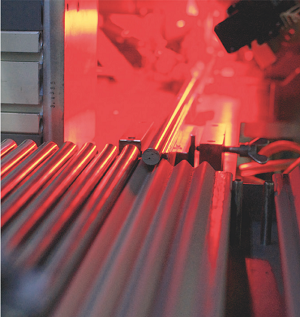
Extruding
The plasticized mixture flows through our extrusion press. At this particular step we bring our rods near their final shape including our famous helical coolant ducts.
Drying
Soaked with plasticizing agent, the rods then need to dry in an air conditioned chamber and special drying-furnaces – the bigger the diameter the longer – before they’re finished in the sinter-hip furnace.
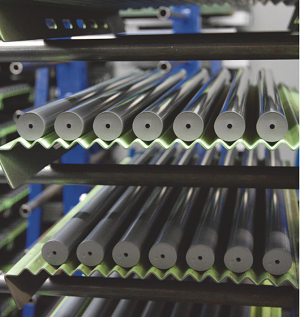
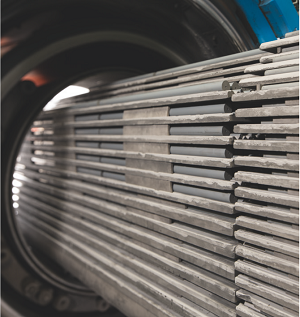
SINTERING
In the sinter-hip process the last plasticizing agents evaporate during the heating process. Finally, at around 1380 C° the cobalt melts, and is embedding the WC grains under hot isostatic pressure. The rods loose up to 25 % of their volume due to shrinkage eliminating porosity.
GRINDING
After passing a last rigorous inspection the rods are then either stocked in our warehouse or refined in our grinding department prior to shipping to our customers.
